Details
- Size: 1,835,000 square feet
- Completion Date: 2020
Team
- Architect: Korth Sunseri Hagey Architects
- Contractor: Vance Brown Builders
- Precast Concrete Manufacturer: Clark Pacific
Awards
-
New Construction, Award of Merit, 2021 SEAOSC Excellence in Structural Engineering Awards
-
All-Precast Concrete Solution Award, 2021 PCI Design Awards
The Escondido Village Graduate Residences (EVGR) at Stanford University was developed to meet the rising demands for on campus graduate student housing. The development adds more than 1,300 units and 2,400 beds, increasing the University’s on-campus graduate housing capacity to 75 percent of its graduate student population. EVGR consists of four new residential buildings, ranging from 6-stories to 10-stories, and totaling 1,835,000 square feet. The project also includes a new 3-story steel framed pavilion building providing amenities in support of the new residential buildings.
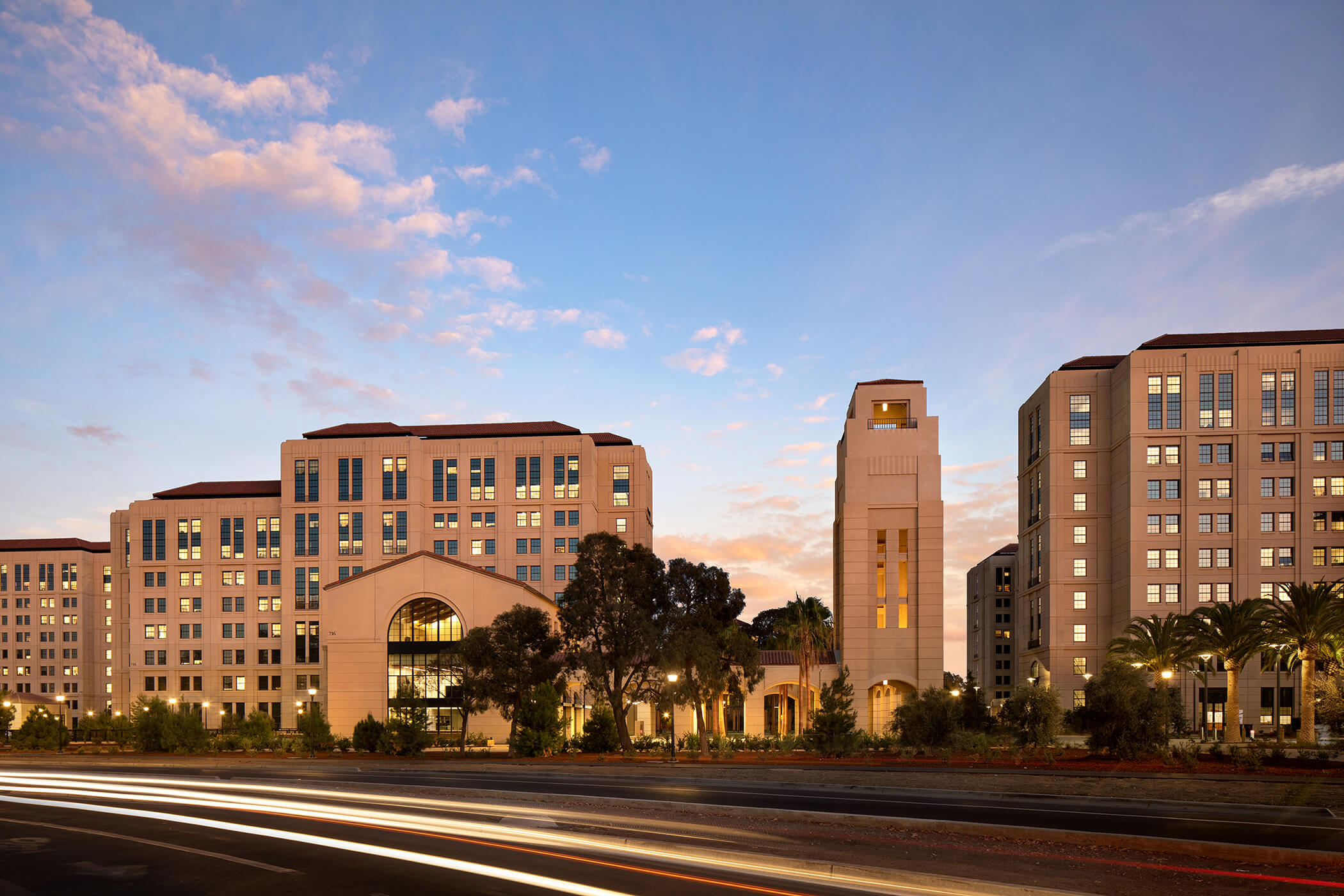
Delivering the Largest Housing Project in University History in Record Time
The design-build team was charged with delivering the project as quickly and with minimal disruption to the surrounding neighbors as possible. These parameters led the team to select a prefabricated, precast concrete system, allowing the majority of building construction to be fabricated off-site within a controlled shop environment, thereby reducing on-site noise, congestion, and field labor. All four buildings were erected in just 11 months, resulting in a 6-month schedule savings for the project.
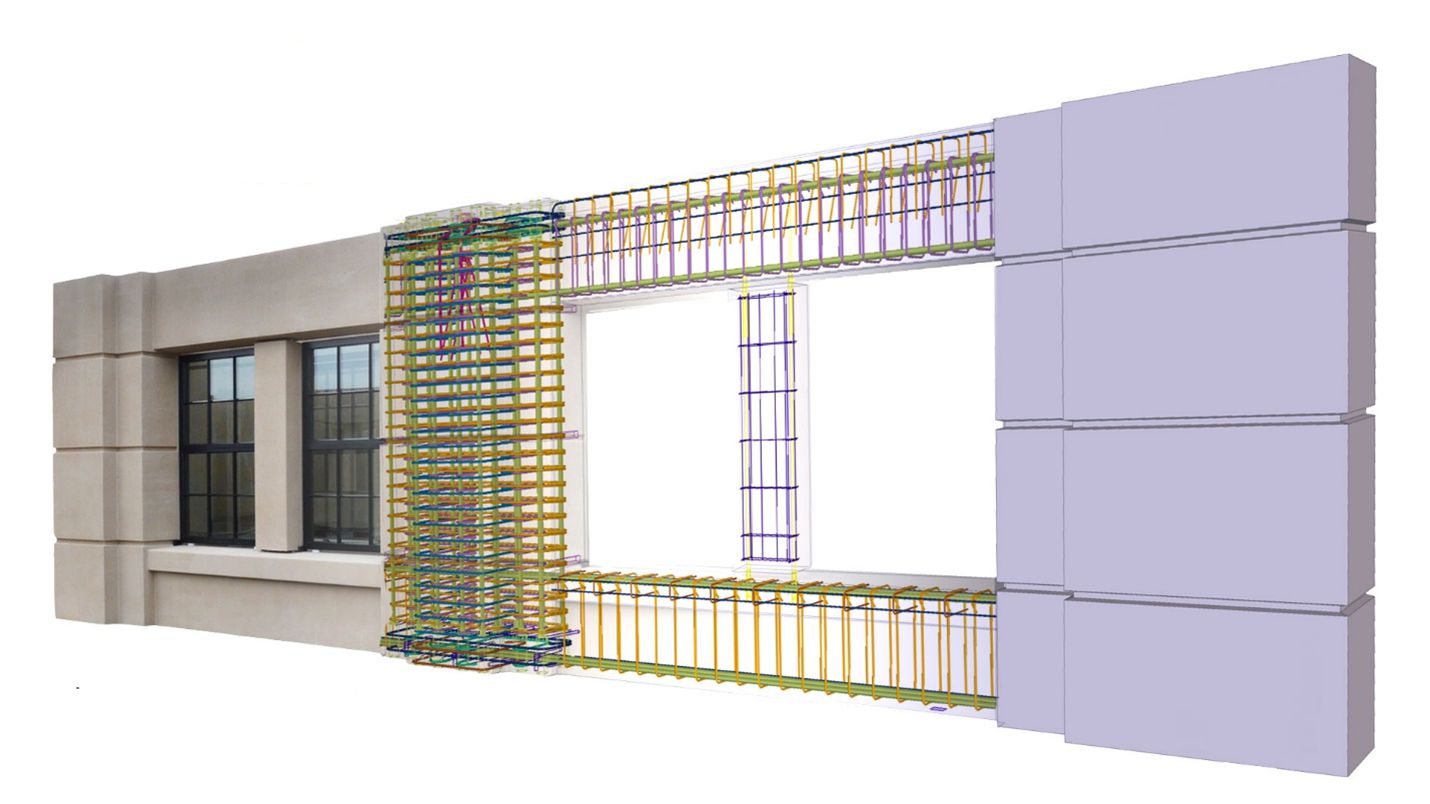
Total Integrated Precast Modular Moment Frame System
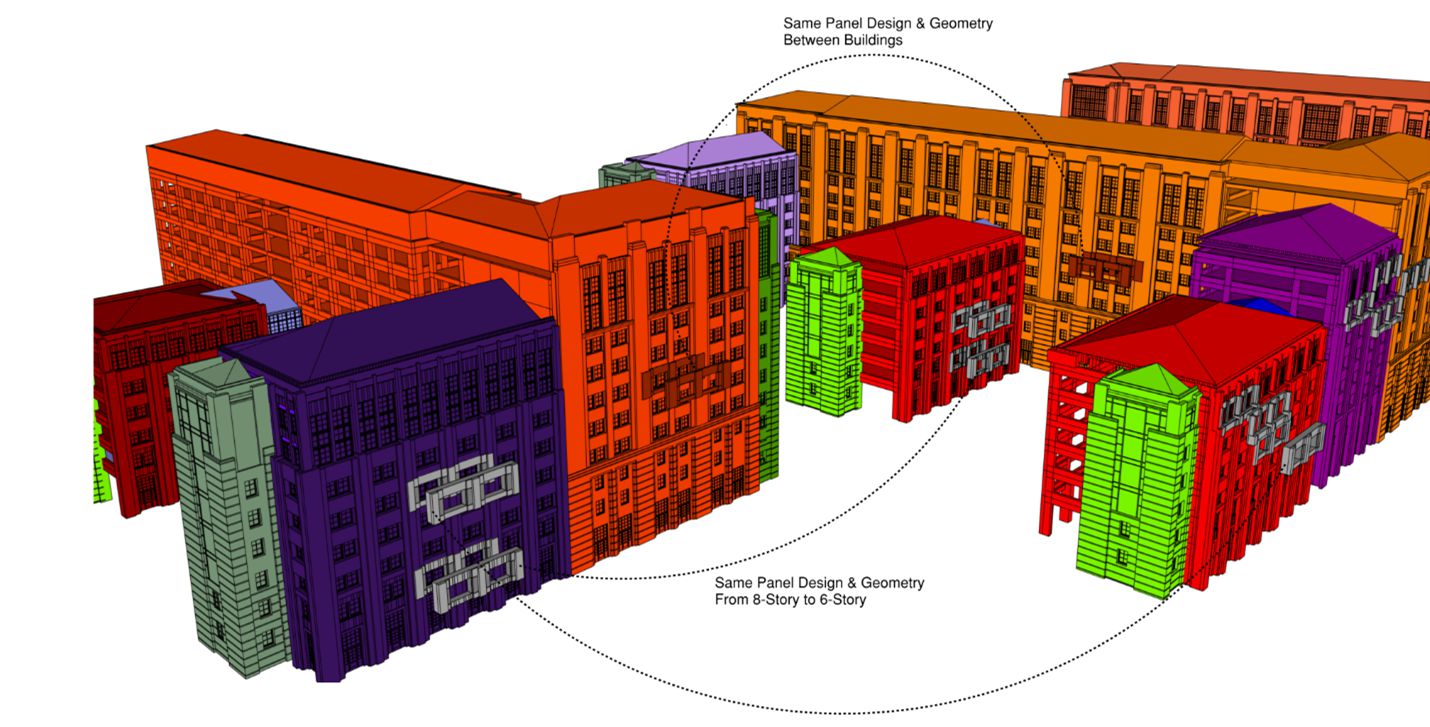
Panel Repetition with the Prefabricated System
Being a total precast solution, the special moment frame structural system was designed with specific consideration for offsite fabrication and quality control, shipment and erection, and efficiency through repetition.
Each residential building is divided into four or five seismically separated structures. Therefore, the “four” residential buildings actually consist of seventeen individual buildings. This improved the seismic performance by avoiding horizontal and vertical structural irregularities such as torsional irregularities and reentrant corners. It also simplified the lateral design by standardizing the design of multiple buildings that have similar configurations. Standardizing the building designs helped optimize the design of the precast panels, minimizing the number of custom forms required for the project.
The repetitive nature of the precast concrete design offered advantages to achieving enhanced seismic performance. Using repetitive exterior panel designs meant that every frame could be a moment frame, resulting in a highly redundant system without incurring additional costs. Furthermore, individual panel designs were replicated across different stories and building segments, which led to panel designs optimized for worst-case locations providing residual strength in other areas.
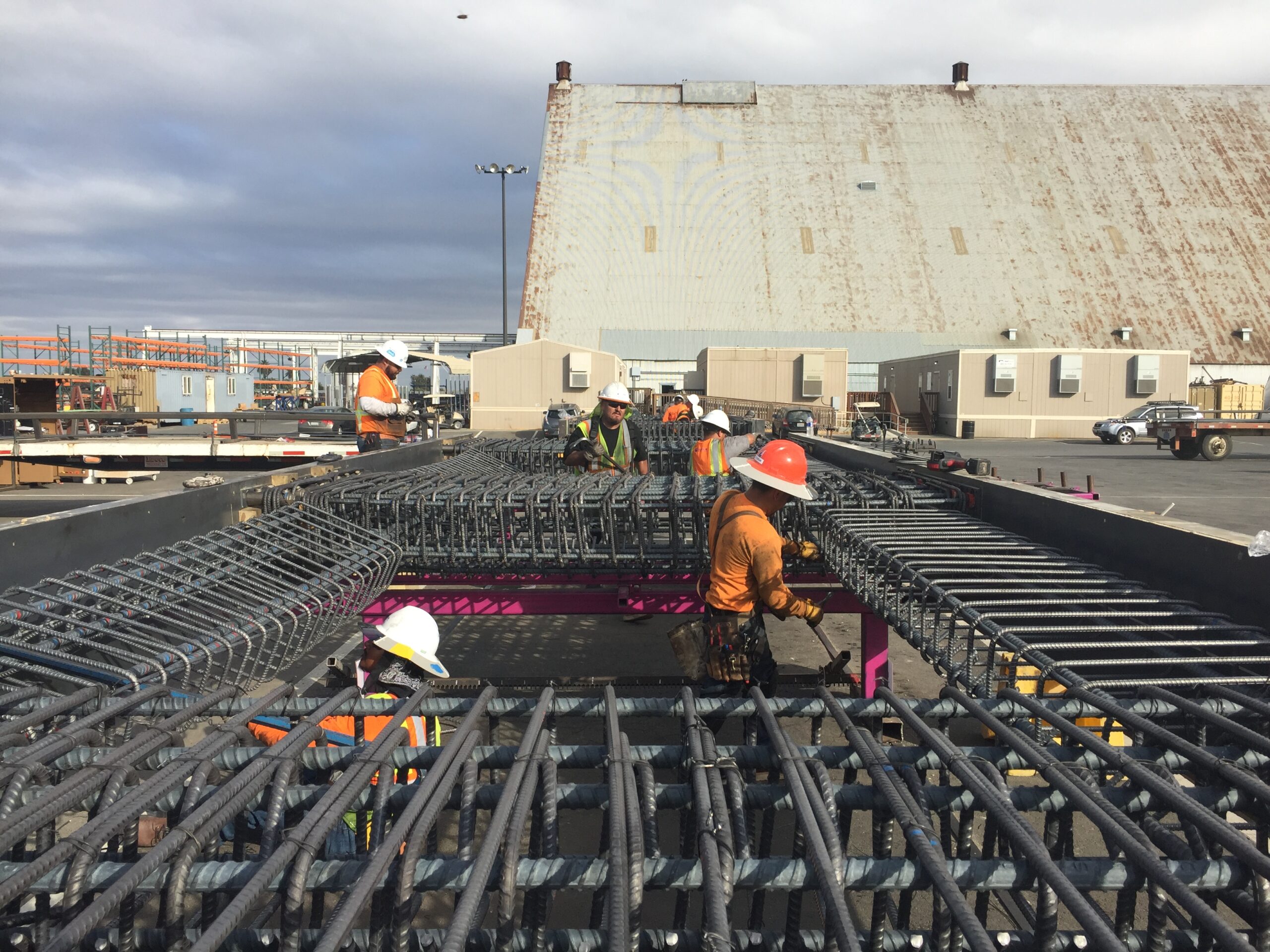
Exterior Moment Frame Panel Production
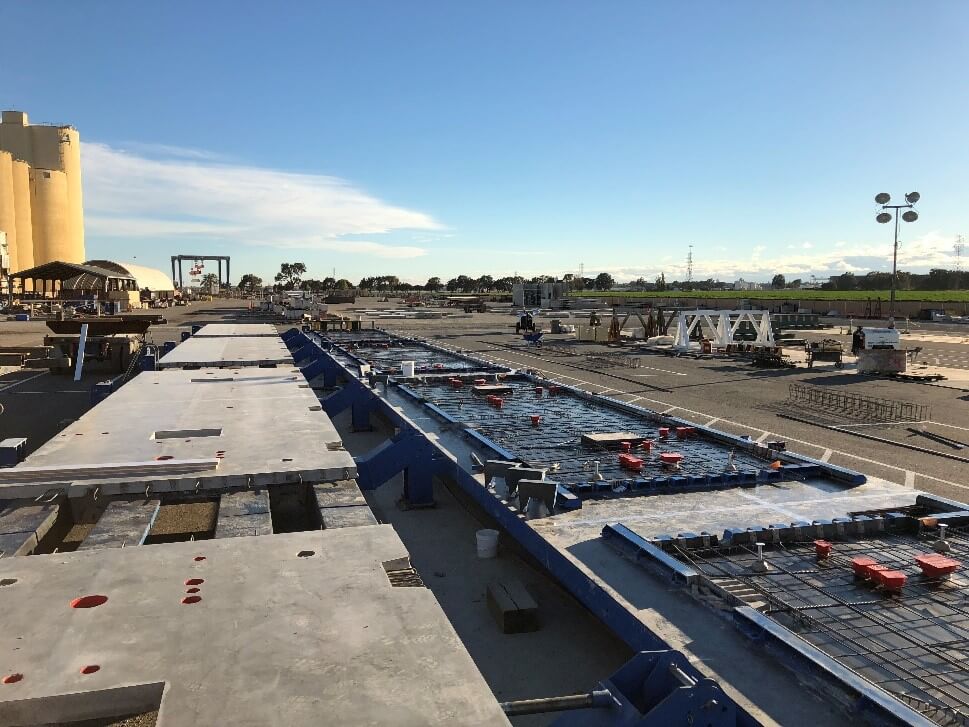
Precast Floor Panel Production at the Clark Pacific Plant
Drawing from concepts used in precast bridge design, JAMA and Clark Pacific reimagined the precast shear transfer connection as an extension of monolithic concrete to eliminate the need for a traditional cast in place topping slab to act as a diaphragm. Untopped precast concrete diaphragms were achieved by connecting the floor planks to each other using interlaced rebar hairpins hooked around a lacer bar running parallel to the plank edges, located at discrete locations along the length of the floor panels. The joints were then filled with grout to create a connection that mimics cast-in-place concrete behavior.
Eliminating topping slabs resulted in an accelerated schedule, reduction in building weight and footing sizes, and reduction in floor to floor and overall building height.
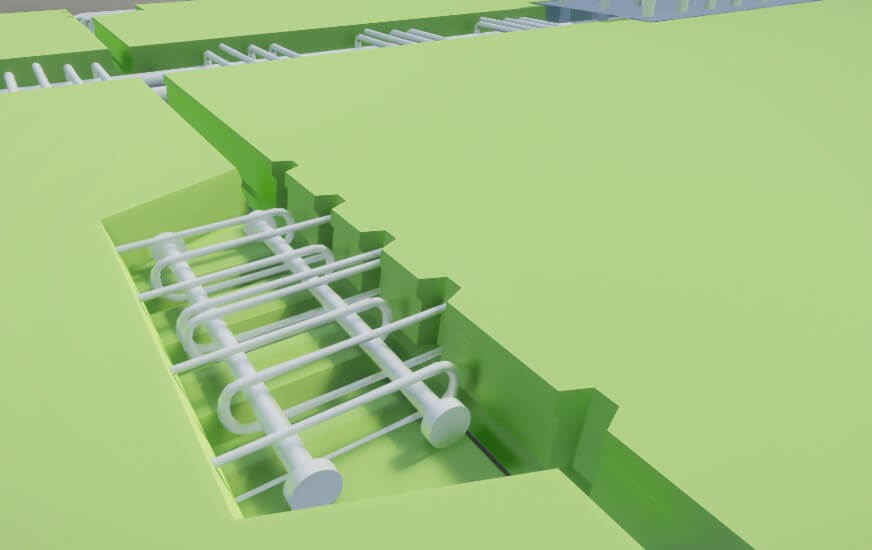
Diaphragm Shear Connection (Render and after installation)
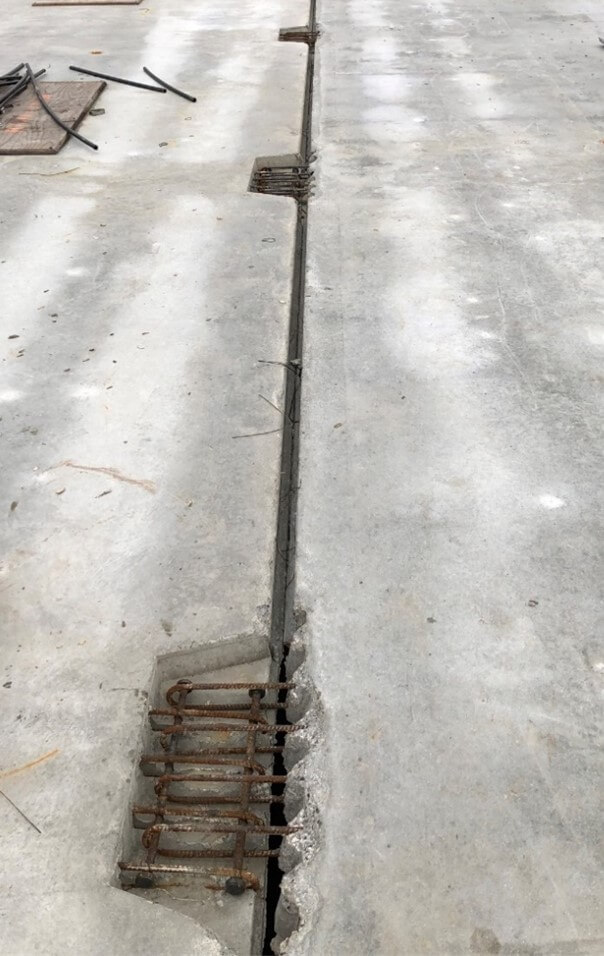
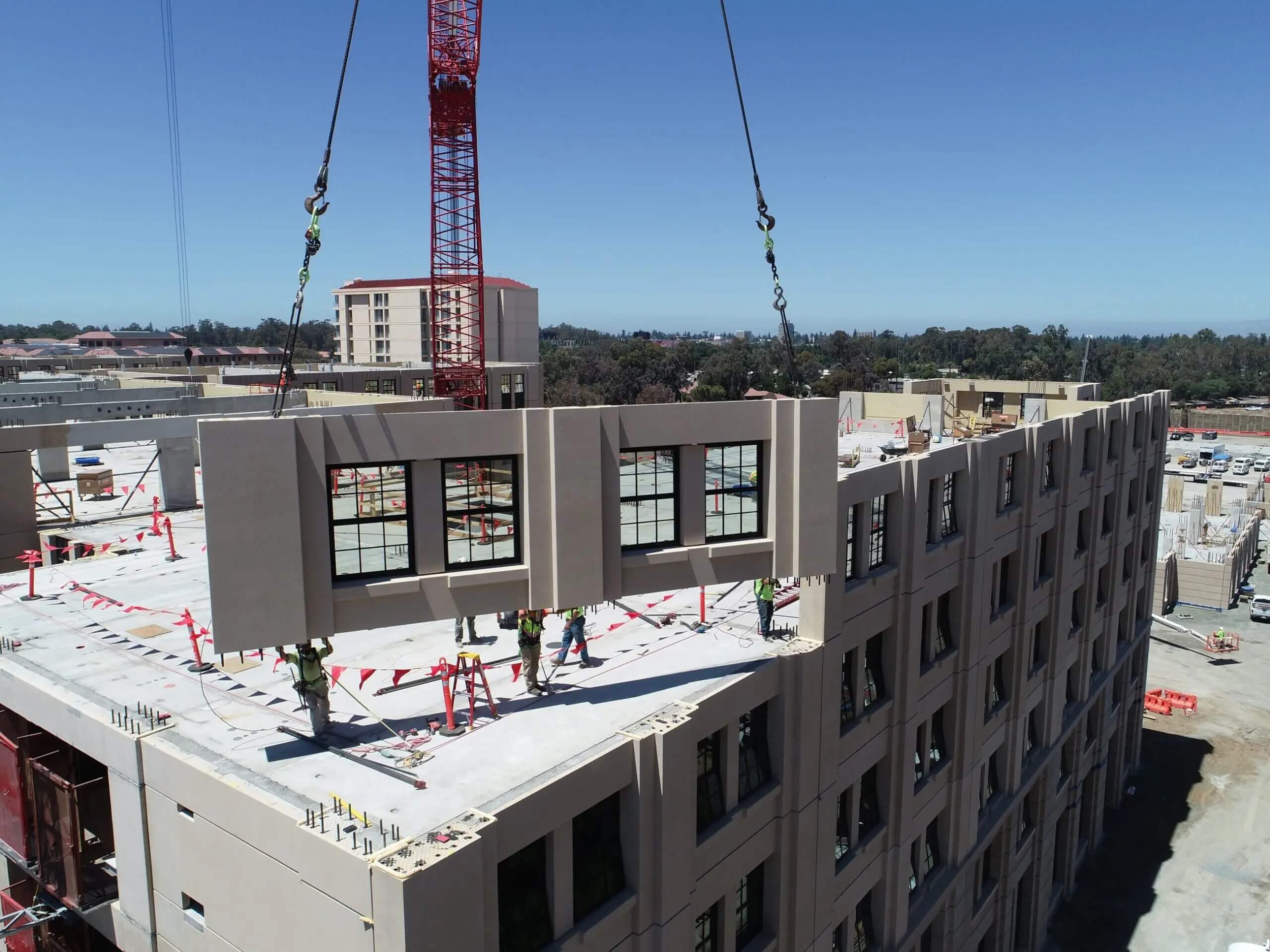
The prefabricated precast concrete solution addressed the combination of the site’s logistical challenges and building performance requirements while reducing the construction schedule and minimizing disruption to the campus. Leveraging the efficiencies inherent with prefabrication and precast concrete resulted in a cost-effective, resilient structural design.
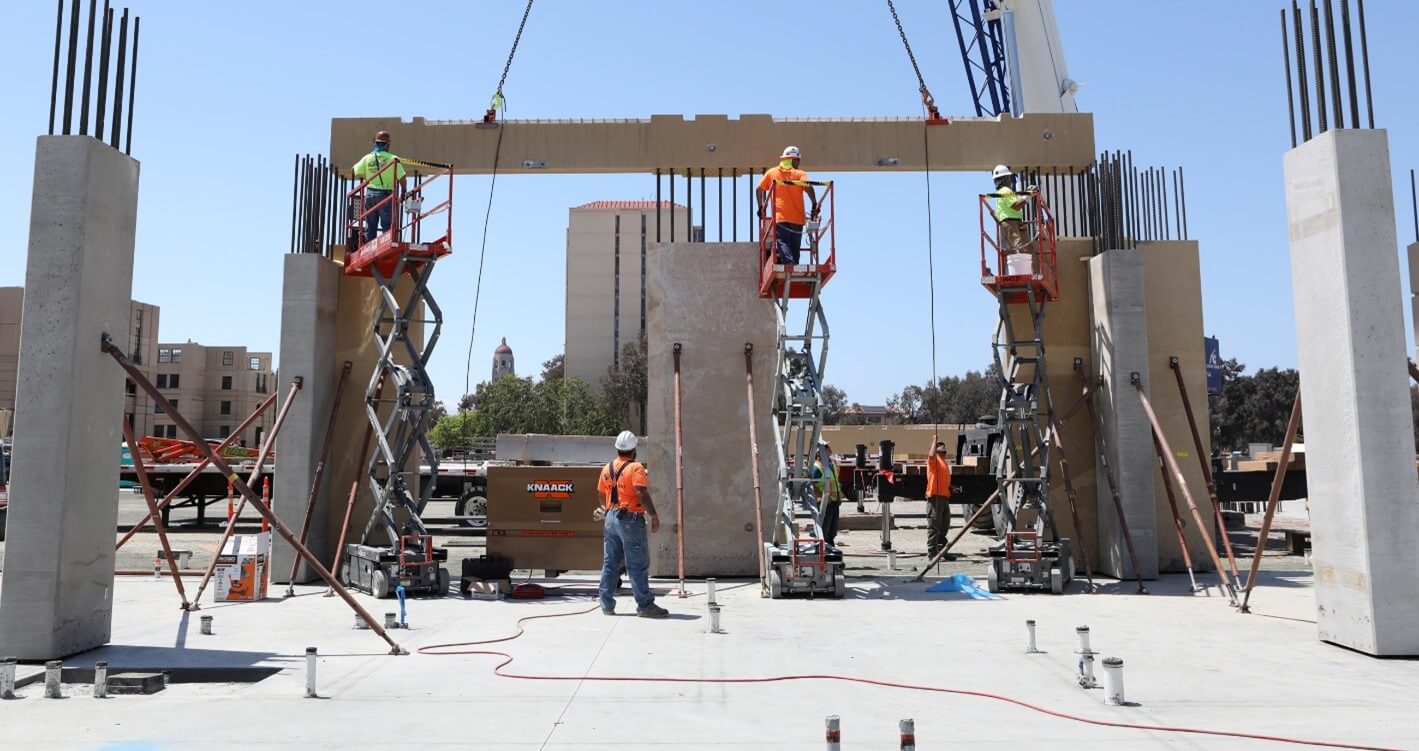
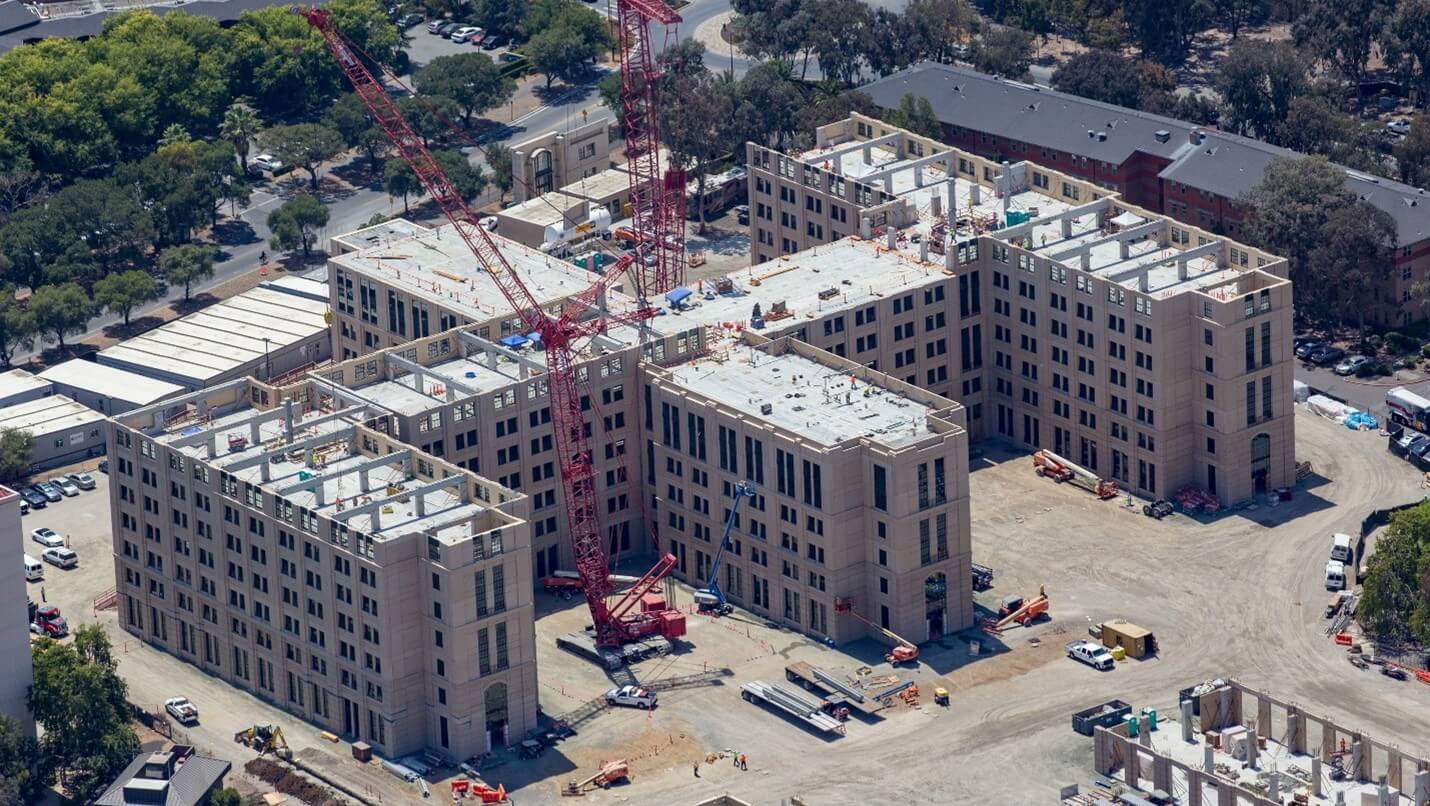
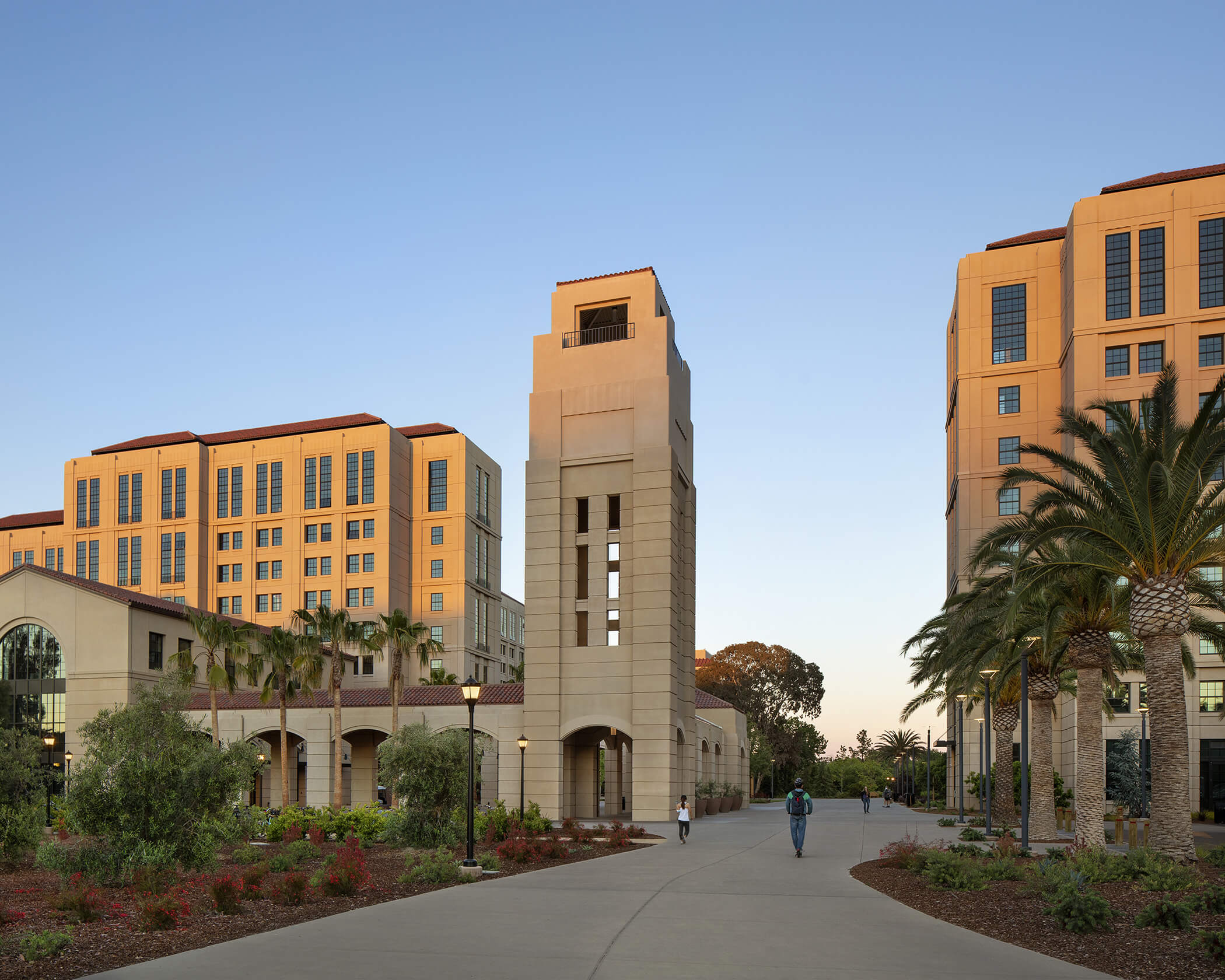
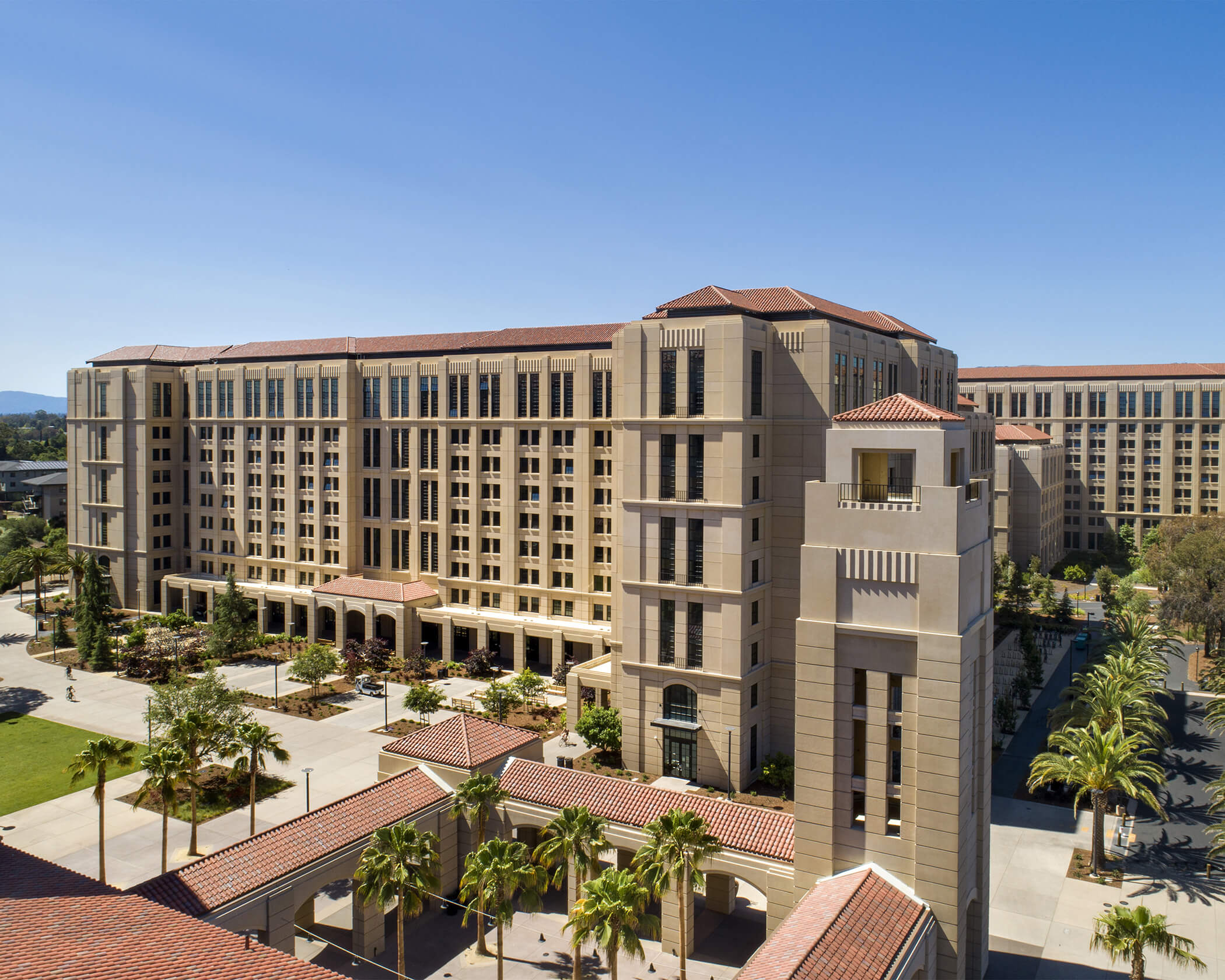