Details
- Size: 270,000 square feet
- Completion Date: 2003
Team
- Architect: Gehry Partners, LLP
- Contractor: Turner Construction / Obayashi Corp.
Awards
-
Building Team of the Year – 2003, American Institute of Architects
-
Building Team Project Grand Award – 2004, Building Design & Construction
-
Excellence Award, Landmark Structures – 2004, Structural Engineers Association of California
Completed in 2003, the Frank Gehry-designed Walt Disney Concert Hall immediately earned worldwide recognition as an architectural masterpiece that firmly established Los Angeles as a cultural destination, pushing the boundaries of architectural form and structural engineering excellence industrywide. Now at 20 years old, the Hall remains an iconic building that continues to evoke inspiration from its visitors admiring the structure, and the musicians that perform within.
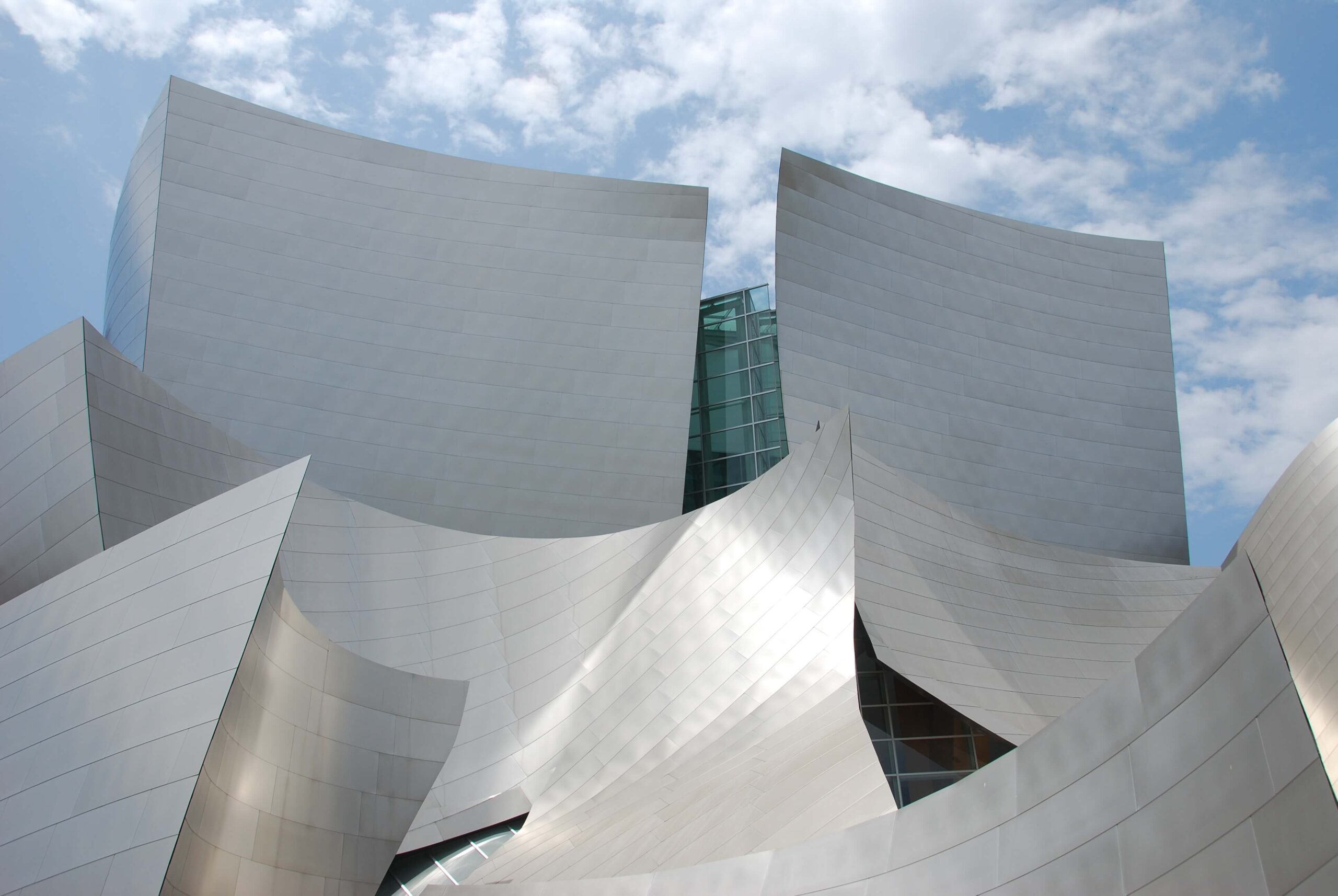
Located at the corner of First Street and Grand Avenue in Downtown Los Angeles, Disney Concert Hall was envisioned from the outset as a catalyst to revitalize the artistic, civic, and social aspects of the area as well as provide a home for the LA Philharmonic. With a composition of metal-clad “sail” planes connected by panels of stainless steel and glass curtainwall and skylights and a steeply raked interior supporting nearly 2,300 seats, the venue has become the cornerstone of LA’s civic life. Other amenities of the complex include three atriums with large, operable glass panels, a multi-purpose pre-concert space for more than 500, a Founders Room with a 50-foot ceiling and skylights, an ensemble studio, retail / dining facilities, and exterior spaces and gardens.
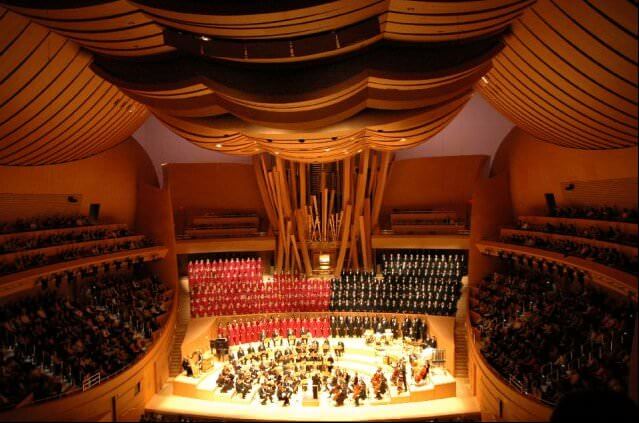
Concert venue
The structural design supporting Gehry’s sculptural forms began with a 2,500-car parking structure completed in 1995. The 70’x58’ below grade theater and additional eight above-grade elements were redesigned after the project had been halted in 1997, but were completed by 2003. Because the garage was completed well in advance of the final design of the other elements, the main concert hall was formed by a 3-dimensional braced-frame in structural steel that sits atop the garage. The braced frame approach, rather than moment frame, proved more efficient and economical under the circumstances.
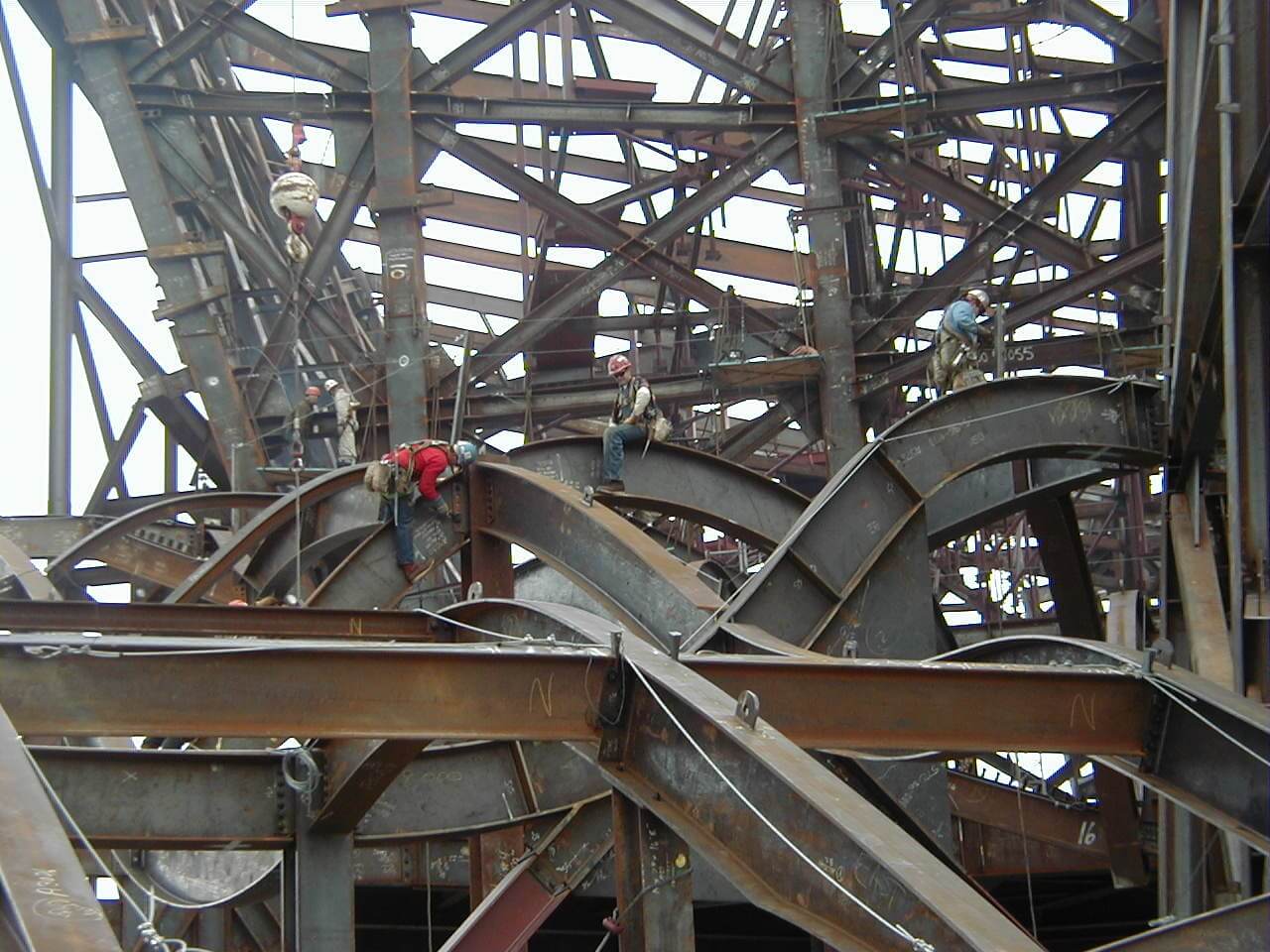
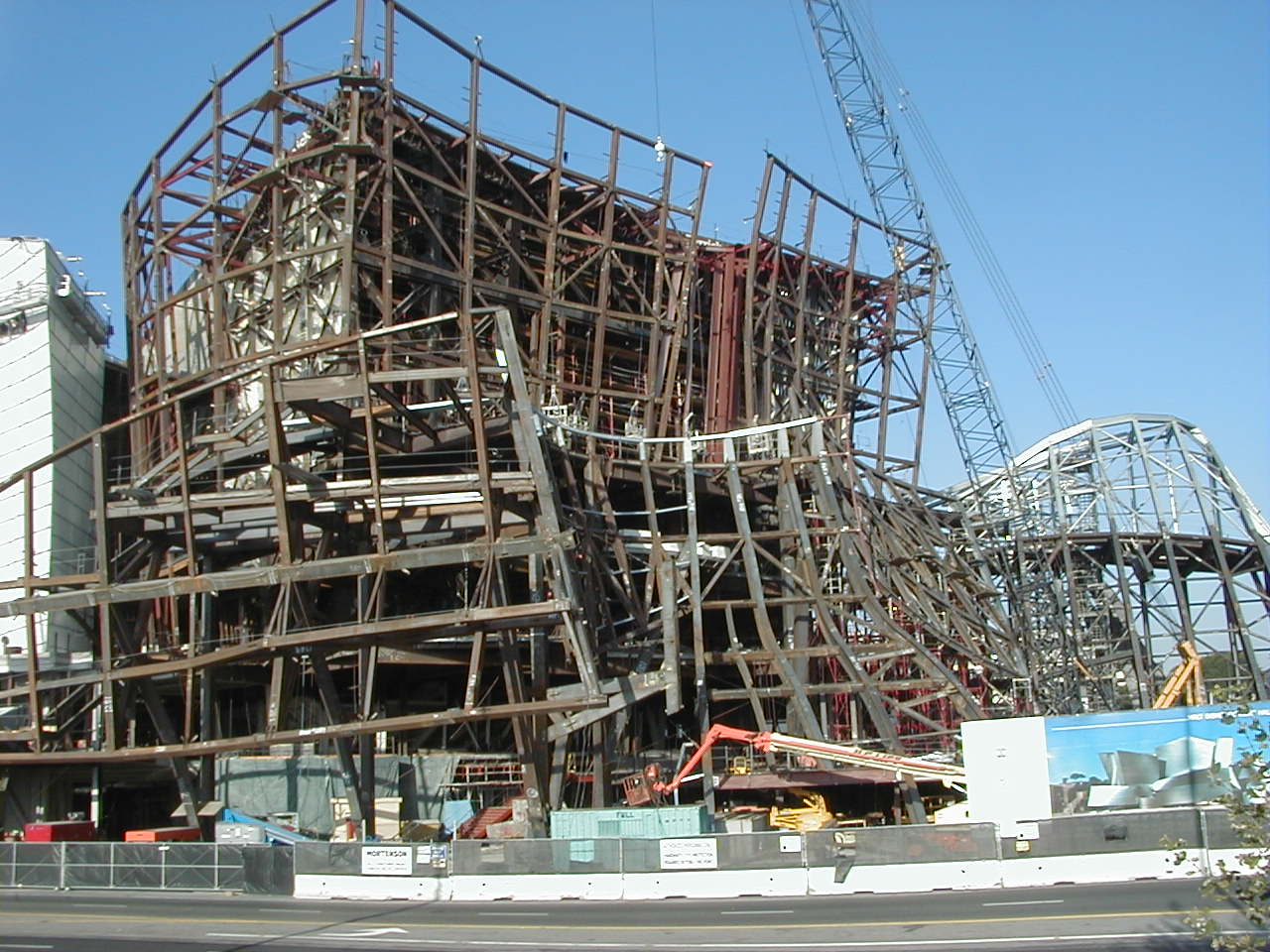
Exposed Structural Steel During Construction
Overall, the steel framing for the Hall is made up of more than 11,000 pieces of structural steel. The exterior skin is made of up of 6,100 individual stainless steel panels. Some columns within the structure deviate off the vertical axis by more than 20 degrees.
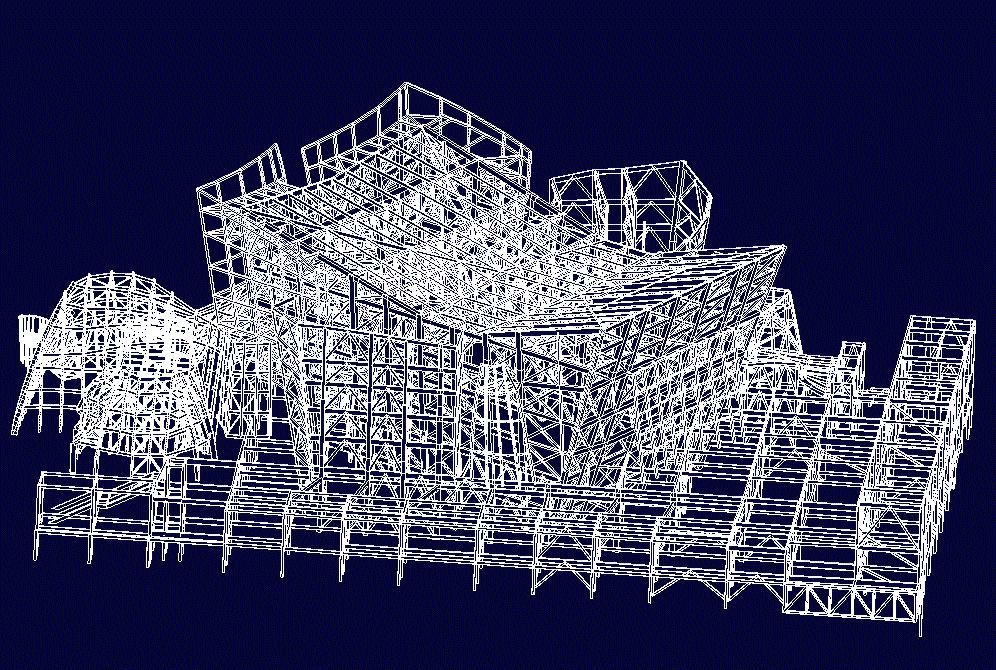
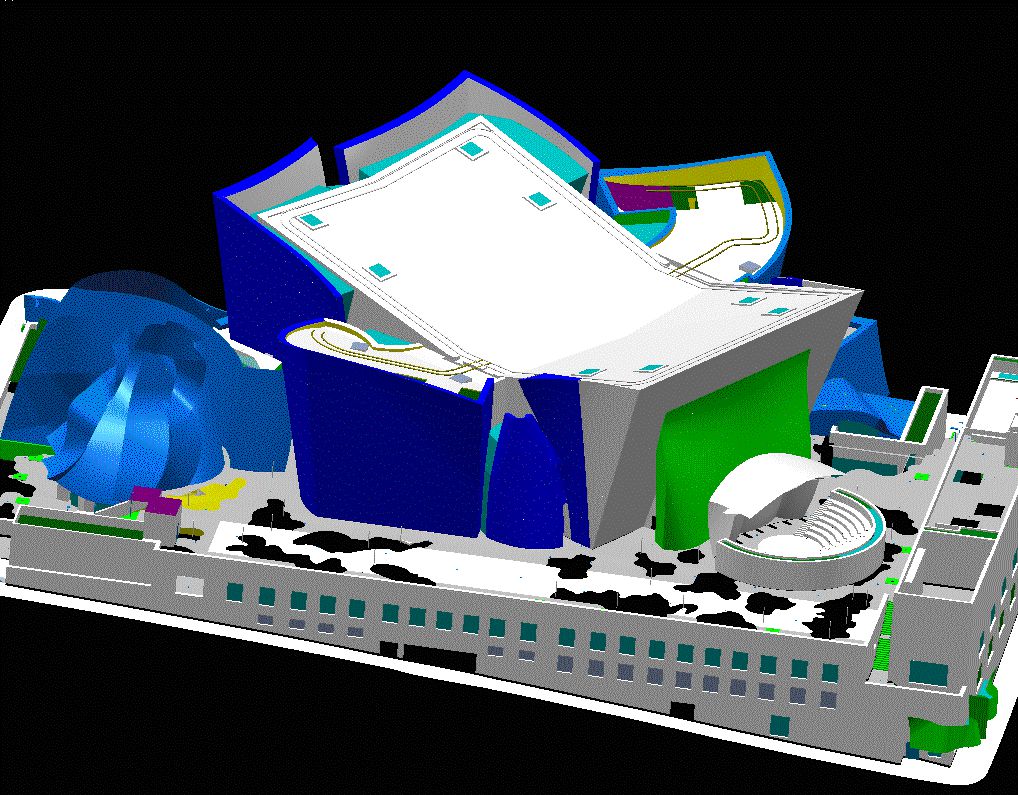
Catia Renderings
Key to engineering the complicated geometry of the building was the adoption of cutting-edge 3D tools and Building Information Technology (BIM), a first for a building of this magnitude and complexity at the time. The structure’s flowing curve with harsh angle skin panels were designed and detailed using CATIA and then fabricated using computer numerically controlled equipment driven by the CATIA model. JAMA staff co-located in Gehry’s office to learn and understand CATIA modeling, and then took the application a step further to accommodate analysis in real-time. Structural analysis via hand-drawings would have been virtually impossible. JAMA’s proprietary computer program manipulated the 3D CATIA model and imported it into SAP-2000 in a format ready to be structurally analyzed.
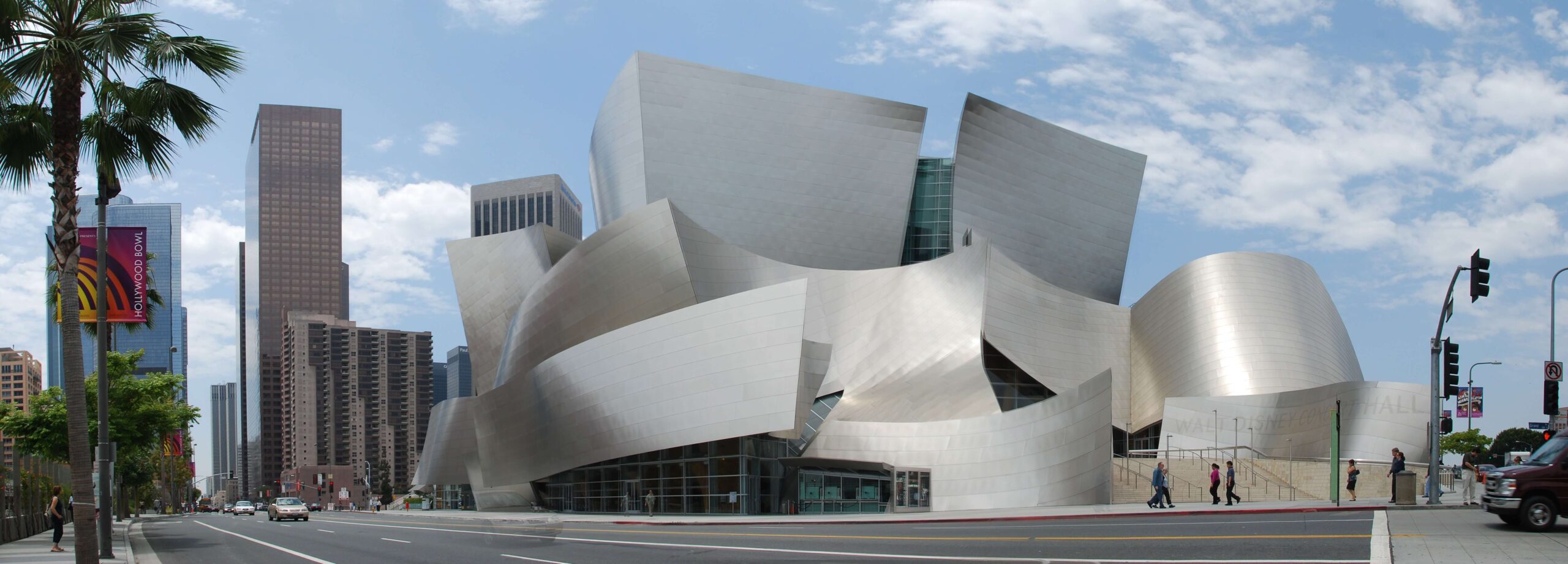
Through the design and construction process JAMA worked alongside Gehry’s team, the contractor, and other disciplines to problem-solve and maintain the schedule and coordination. In addition to CATIA, X-Steel, a 3D steel detailing program, was vital to keeping steel fabrication ahead of field work. Even with all of the unique elements, many standard construction details were applied in order to keep costs under control.
The technologies developed to deliver this building pushed the boundaries of structural engineering and established JAMA as an industry leader in innovative problem-solving using a technology-driven process to design. JAMA continues to lead by embracing new and advanced technologies and incorporating them into our workflow to deliver efficient structural solutions.